The cast iron ball, while seemingly simple, is an engineering marvel that has stood the test of time. This article delves into the multifaceted world of cast iron balls, exploring their production, applications, and the expertise surrounding their use.
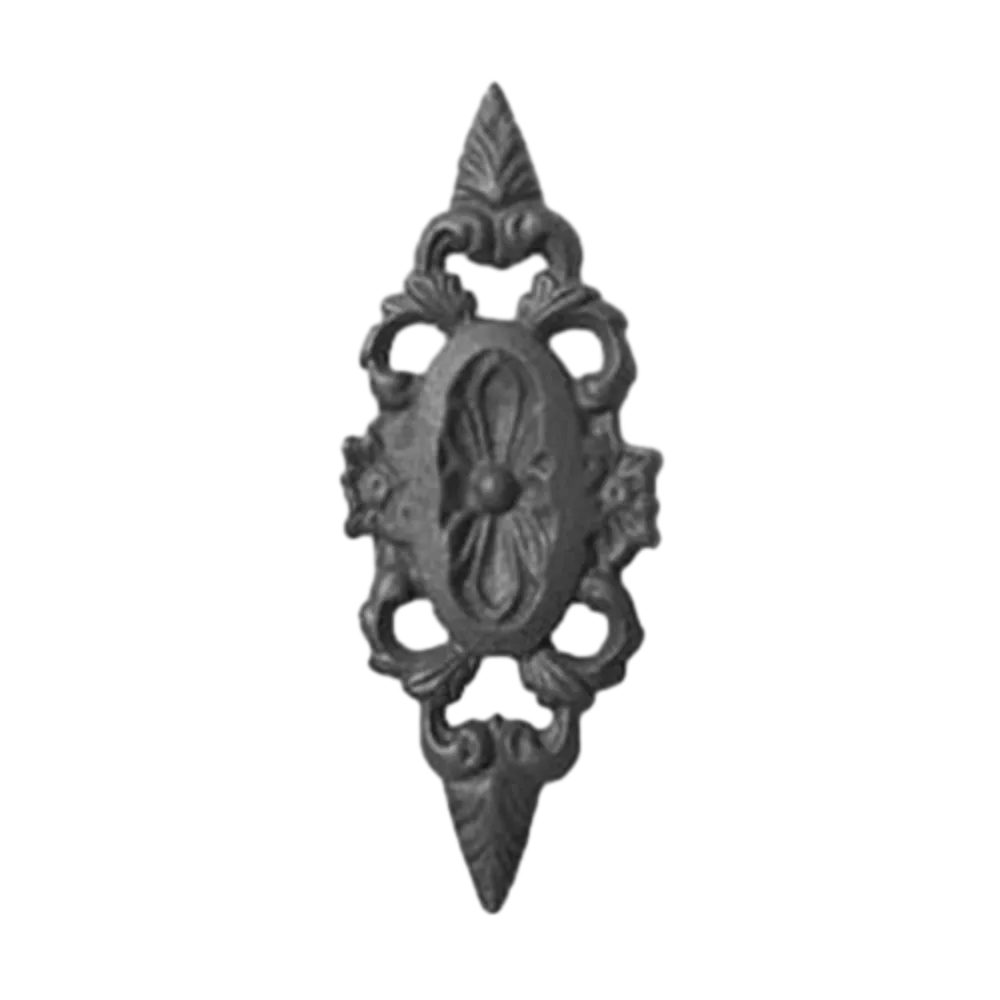
Cast iron balls are primarily produced through a method known as casting, where molten iron is poured into molds. This process demands precision and expertise to ensure the final product is uniform and durable. The type of cast iron used, typically gray iron or ductile iron, contributes significantly to the ball's characteristics. Gray iron, known for its excellent machinability and strength, is often used where cost-efficient production is paramount, while ductile iron offers enhanced shock absorption and tensile strength, making it suitable for more demanding applications.
The versatility of cast iron balls is evident in their wide range of applications. In the mining industry, they are utilized as grinding media within ball mills to break down ores into finer particles for extraction.
The wear resistance and hardness of cast iron make these balls ideal for pulverizing even the toughest materials. Similarly, in cement production, cast iron grinding balls help in the efficient crushing of clinker into powder, facilitating the creation of high-quality cement.

Cast iron balls also play a vital role in the manufacturing of pyrolytic graphite, where they are used in high-temperature environments due to their ability to retain integrity under thermal stress. Industrial processes such as coal pulverization heavily rely on cast iron balls because of their durability and ability to withstand abrasion and impact.
cast iron ball
The expertise involved in producing high-quality cast iron balls cannot be understated. Foundries employ metallurgists who meticulously balance the carbon and silicon content during production to achieve the desired properties. The spheroidization process, essential for ductile iron, requires a precise addition of magnesium to transform the graphite structure, enhancing ductility and strength. Quality control is a critical aspect; each batch undergoes rigorous testing to ensure conformity to industry standards.
For those seeking to understand the complexities of cast iron ball production, visiting a foundry offers invaluable insight. Observing the melting, casting, and cooling stages of production can provide a firsthand experience of the precision and skill involved. Talking with seasoned metallurgists can deepen one's comprehension of the science behind each phase, from the chemical composition of the iron to the specific requirements of different industries.
Trust in a brand’s ability to deliver high-quality cast iron balls lies in both certification and reviews from satisfied customers across various industries. Reputable manufacturers will possess ISO certifications, reinforcing their commitment to maintaining standards. Customer testimonials often highlight the reliability and longevity of the cast iron balls, further solidifying the manufacturer's credibility.
In conclusion, the cast iron ball is more than just a spherical object; it is a testament to human ingenuity and expert craftsmanship. Its enduring presence in numerous industries underscores its significance and reliability. To understand the true value of cast iron balls, one must appreciate the detailed processes of their creation, the expertise of those who produce them, and the trust that businesses place in these essential components. Through a combination of controlled manufacturing processes and expert knowledge, cast iron balls continue to serve critical roles in industrial applications worldwide, offering unmatched performance and durability.