Cast iron casting remains a pivotal process in the manufacturing industry, prized for its durability, versatility, and economic advantages. For anyone looking to delve into this realm, understanding the intricacies of cast iron casting can offer significant benefits.
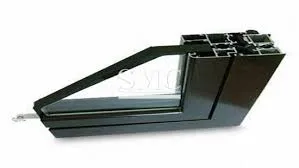
Experience has shown that cast iron casting is unmatched when it comes to producing complex shapes with precision. Manufacturing professionals acknowledge the process's efficiency in delivering components with intricate geometries without requiring extensive machining post-casting. This efficiency saves time and reduces production costs, enabling manufacturers to offer their products at competitive prices without compromising quality. Additionally, the ease of casting combined with its ability to replicate detailed designs makes it a favorite in industries like automotive, construction, and machinery.
The expertise involved in cast iron casting cannot be overstated. The process requires a profound understanding of metallurgy and material science. Cast iron, a group of iron-carbon alloys with a higher carbon content, offers various grades, each having unique properties that cater to specific applications. For instance, gray iron, with its excellent thermal conductivity and damping properties, finds extensive use in engine blocks and machinery bases. Ductile iron, on the other hand, provides superior strength and flexibility, rendering it suitable for pressure-containing applications like pipes and pumps. An expert's role is crucial to select the appropriate iron type and ensure the desired mechanical properties are achieved through controlled cooling and alloying.
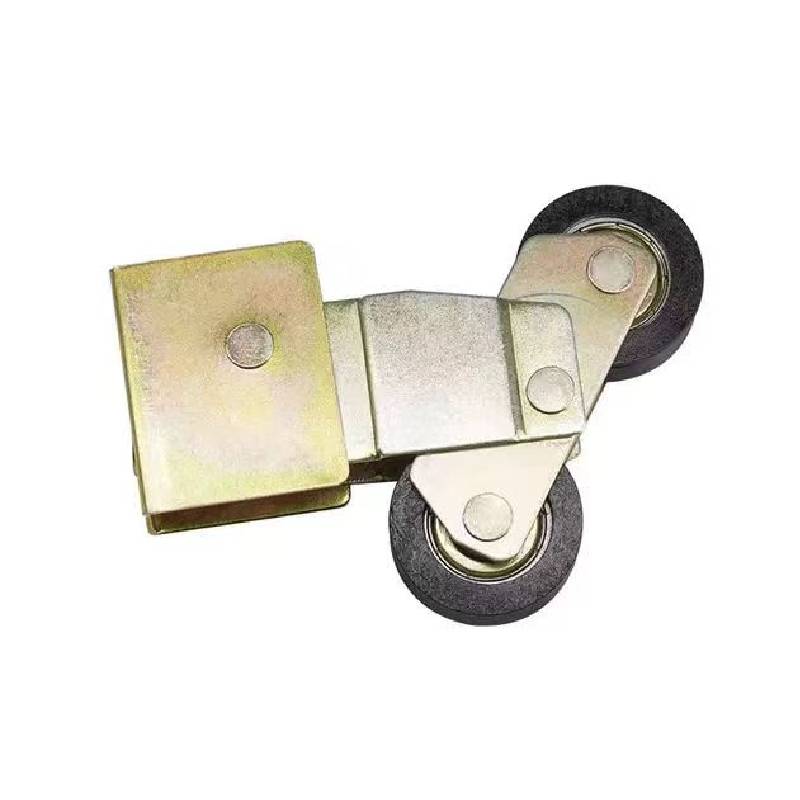
Authoritativeness in cast iron casting is evident through the industry's reliance on established standards and protocols. Renowned organizations like ASTM and ISO have set rigorous benchmarks for cast iron products, ensuring consistency and reliability across global markets. Companies engaged in cast iron casting must adhere to these standards, which govern aspects such as chemical composition, tensile strength, and hardness. Compliance with such standards not only affirms the quality of the cast products but also enhances a company's reputation and credibility in the international sphere.
cast iron casting
Trustworthiness is a cornerstone of any successful venture in the cast iron casting business. Customers must be able to trust that the components they receive will perform as expected and meet the specific requirements of their applications. This trust is cultivated through rigorous quality assurance processes and comprehensive material testing. Non-destructive testing methods, such as ultrasonic testing and radiographic inspection, are employed to detect internal defects and ensure the integrity of the castings. Furthermore, manufacturers often provide detailed certifications and documentation, attesting to the quality and compliance of their products.
Cast iron casting also contributes significantly to sustainability objectives within manufacturing sectors. The process allows for extensive recycling of materials, minimizing waste and lowering environmental impact. Many companies have adopted eco-friendly casting techniques, prioritizing the use of recycled scrap iron and implementing cleaner production technologies to reduce emissions. Such initiatives align with global sustainability goals and enhance a company's environmental stewardship, appealing to environmentally conscious consumers and stakeholders.
In conclusion, the realm of cast iron casting is rich with opportunities for innovation and excellence. By leveraging experience, expertise, authoritativeness, and trustworthiness, companies can not only excel in the competitive manufacturing landscape but also contribute positively to the industry's evolution. Embracing advancements in casting technologies and adhering to best practices will ensure that cast iron casting continues to be a linchpin of industrial success for years to come.