In the world of industrial and domestic applications, cast iron components have carved out a venerable niche.
These rugged and resilient parts are integral in a range of products from cooking wares to automotive and machinery components. Their widespread usage is not coincidental but rather is deeply rooted in their unparalleled properties which align perfectly with practical and commercial needs.
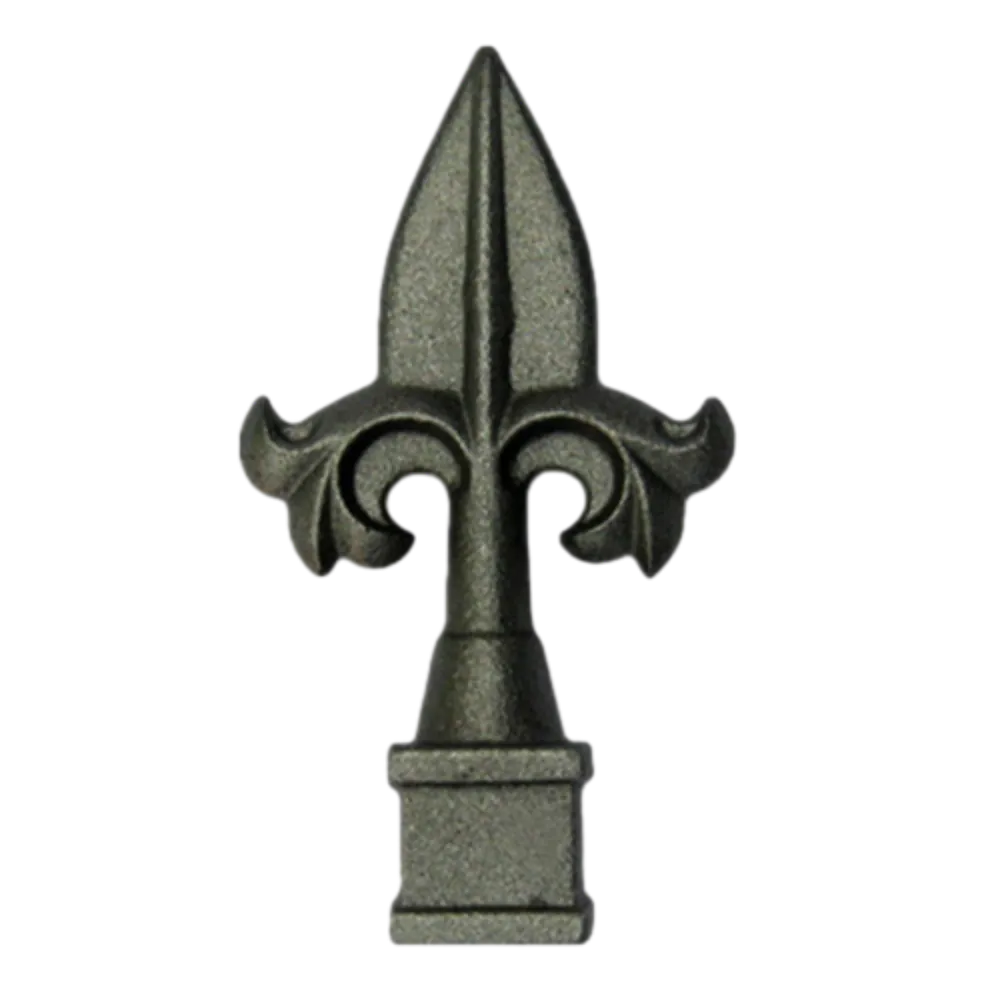
Cast iron is renowned for its remarkable strength, wear resistance, and ability to withstand high temperatures. These characteristics are derived from its unique composition; primarily iron, carbon, and silicon, that give it a distinctive microstructure. Unlike steel, which is more malleable, cast iron contains higher levels of carbon, which forms graphite flakes during cooling. This graphite configuration bestows cast iron with its hallmark brittleness, but also grants exceptional compressive strength and thermal conductivity, making it ideal for heat-intensive applications like stove parts, engine blocks, and brake drums.
When it comes to expertise in manufacturing cast iron components, precision casting is an art that demands in-depth knowledge and technical skill. The process begins with creating a mold, usually made from sand, which defines the external shape. The molten iron is carefully poured into this mold, where it solidifies and takes form. This method allows for the production of intricate shapes and sizes with remarkable accuracy. Those experienced in metallurgy understand that controlling the cooling rate is critical to preventing undesirable stress and ensuring the component's integrity.
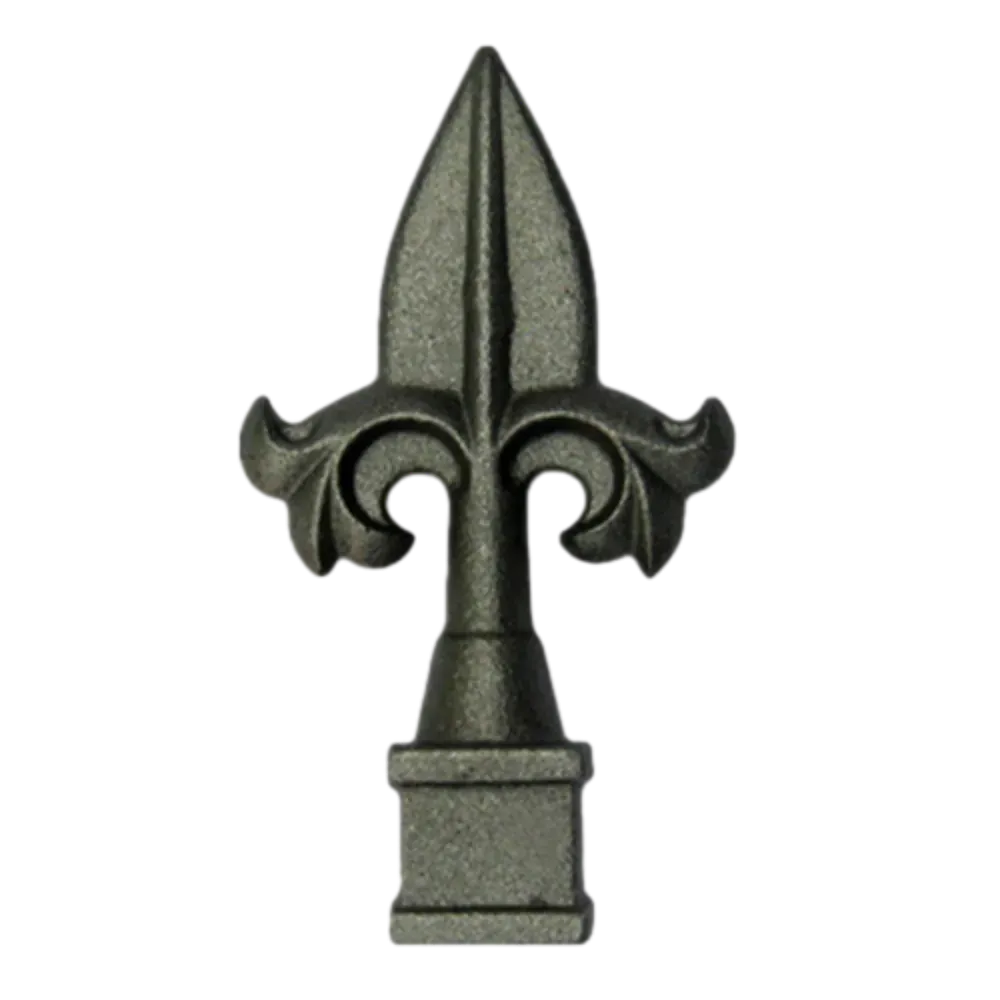
The manufacture of cast iron components also carries a considerable degree of authoritativeness, as industry standards dictate the composition and quality measures required for different applications. Organizations such as ASTM International set stringent specifications that manufacturers must adhere to, ensuring consistency and reliability across the board. Certified producers thus contribute to a network of trust and quality assurance, reinforcing the authoritative nature of cast iron in industrial settings.
cast iron component
The trustworthiness of cast iron components is further reinforced by their historical performance across numerous industries. In construction, for example, cast iron pipes and architectural details have stood the test of time, proving their durability and reliability over decades. Likewise, in automotive and heavy machinery, the ability of cast iron to absorb vibration and noise while offering longevity under stress is well-documented. Users and manufacturers consistently report satisfaction with products that successfully incorporate these components, knowing they are investing in proven reliability.
Despite their advantages, choosing the right type of cast iron—whether gray iron, ductile iron, or others—is paramount to capitalizing on the material’s properties. Each variant has specific attributes. Gray iron is popular for its excellent machinability and damping capabilities, while ductile iron offers more flexibility and impact resistance due to its spheroid-shaped graphite inclusions.
To leverage these components effectively in new product designs, collaboration with experienced manufacturers can provide insights into materials selection, design considerations, and cost optimization. A detailed understanding of casting processes and standards further enhances the creation of components that not only meet but exceed technical and commercial specifications.
In summary, cast iron components are indispensable in multiple domains due to their robustness, thermal properties, and historical reliability. Anchored by industry standards and best practice guidelines, they continue to offer unmatched value in both traditional and innovative applications. For businesses aiming to integrate these components, partnering with credible suppliers can ensure quality and foster innovations that drive industry growth and consumer satisfaction.