Metal casting is an ancient technique that melds tradition with cutting-edge innovation, offering unmatched precision and customizability for modern manufacturing processes. Over the centuries, this method has evolved, enhanced by technological advancements, yet its fundamental principles have remained steadfast. For businesses seeking to leverage the profound capabilities of metal casting, understanding the nuances of this process is imperative.
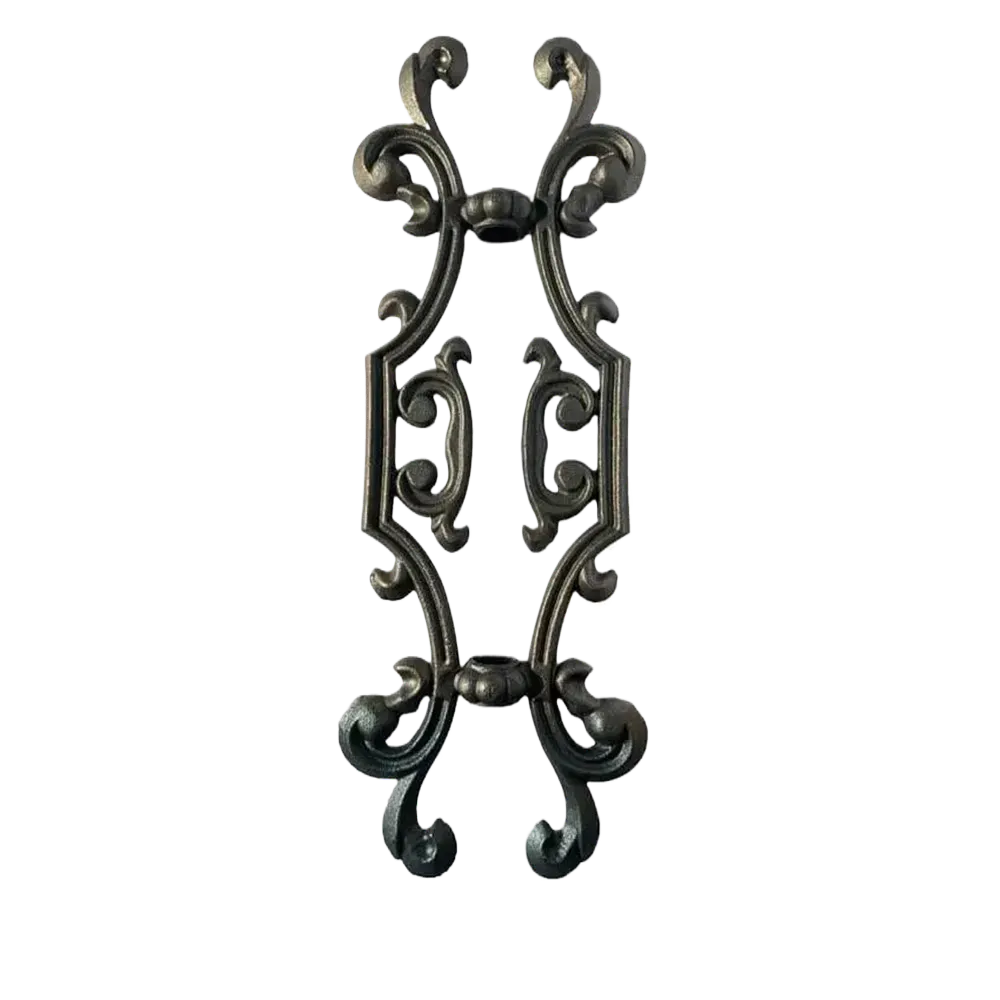
Metal casting begins with a mold, generally crafted from sand, plaster, or ceramic, chosen based on the metal's melting point and the complexity of the design. Expert mold designers invest vast expertise to ensure the mold will withstand the molten metal’s pressure and temperature. This mold forms the negative impression of the final product, meticulously shaped to accommodate everything, from simple components to complex industrial products, a testament to the versatility and skill inherent in casting.
In the realm of expertise,
one’s choice of metal significantly influences the casting process. Aluminium, for example, provides a lightweight yet robust solution popular in automotive and aerospace industries, whereas steel or iron offers unparalleled durability for heavy machinery. Lead-free alloys are gaining traction in the consumer goods sector, reflecting a shift towards environmentally conscientious practices. Balancing these choices demands a profound understanding of the material properties, attuned to specific industrial requirements.
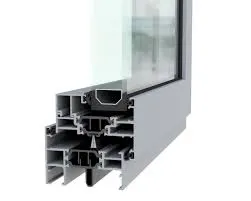
Trustworthiness is deeply rooted in the metal casting industry's commitment to quality and consistency. Manufacturers adhere to stringent industry standards, from ASTM to ISO certifications, ensuring products withstand stressors and meet specific performance criteria. Furthermore, advanced testing methods, including X-ray radiography and ultrasonic testing, provide additional layers of quality assurance. These sophisticated techniques unveil hidden flaws that might compromise structural integrity, fostering customer confidence through a transparent quality evaluation process.
The authority of metal casting in production is underscored by the breadth of its applications. It extends beyond traditional manufacturing into novel areas such as bespoke 3D printing, where digital blueprints are translated into precision-engineered components. Collaborations with industries like automotive and aerospace further reinforce casting's authoritative stance, as these sectors demand high-strength, lightweight components that metal casting readily provides. By embracing technological advances, these industries validate metal casting's timelessness and its critical role in modern manufacturing.
metal casting
When discussing the experience aspect, consider the collaboration between engineers and casting technicians. Their shared knowledge turns initial design concepts into tangible products, offering clients an unparalleled depth of insight throughout the production cycle. This teamwork ensures that each casting is optimized for performance while minimizing waste, a critical commitment to sustainability.
In terms of sustainability, movers and shakers in metal casting are pioneering eco-friendly practices by recycling materials and reducing energy consumption. Innovations like efficient furnace designs and alternative energy sources are revolutionizing the industry, making significant strides towards reducing the carbon footprint. Such initiatives demonstrate a conscientious shift towards sustainable manufacturing, which will only increase as global emphasis on environmental stewardship intensifies.
Aspiring companies considering metal casting must assess and integrate these multifaceted aspects into their production strategies. With the substantial impact of casting products on sectors such as infrastructure, energy, and even consumer electronics, it’s essential to align with partners who exhibit expertise and experience. Firms who prioritize transparency, quality, and environmental responsibility stand poised to lead in this expansive field.
Conclusively, metal casting represents a blend of time-honored techniques and futuristic innovation. Companies aiming to incorporate metal casting in their manufacturing must consider factors from material selection to quality assurance and sustainability efforts. This intricate dance between tradition and modernization epitomizes the journey of metal casting a field ever-evolving, yet fundamentally grounded in principles of precision, expertise, and environmental consciousness.