Metal leaves for welding have emerged as crucial components in modern industrial practices. As welding evolves, so do the materials and techniques that accompany it, and metal leaves are at the forefront of these advancements. With their unique properties and application potential, metal leaves offer a viable solution to many welding challenges.
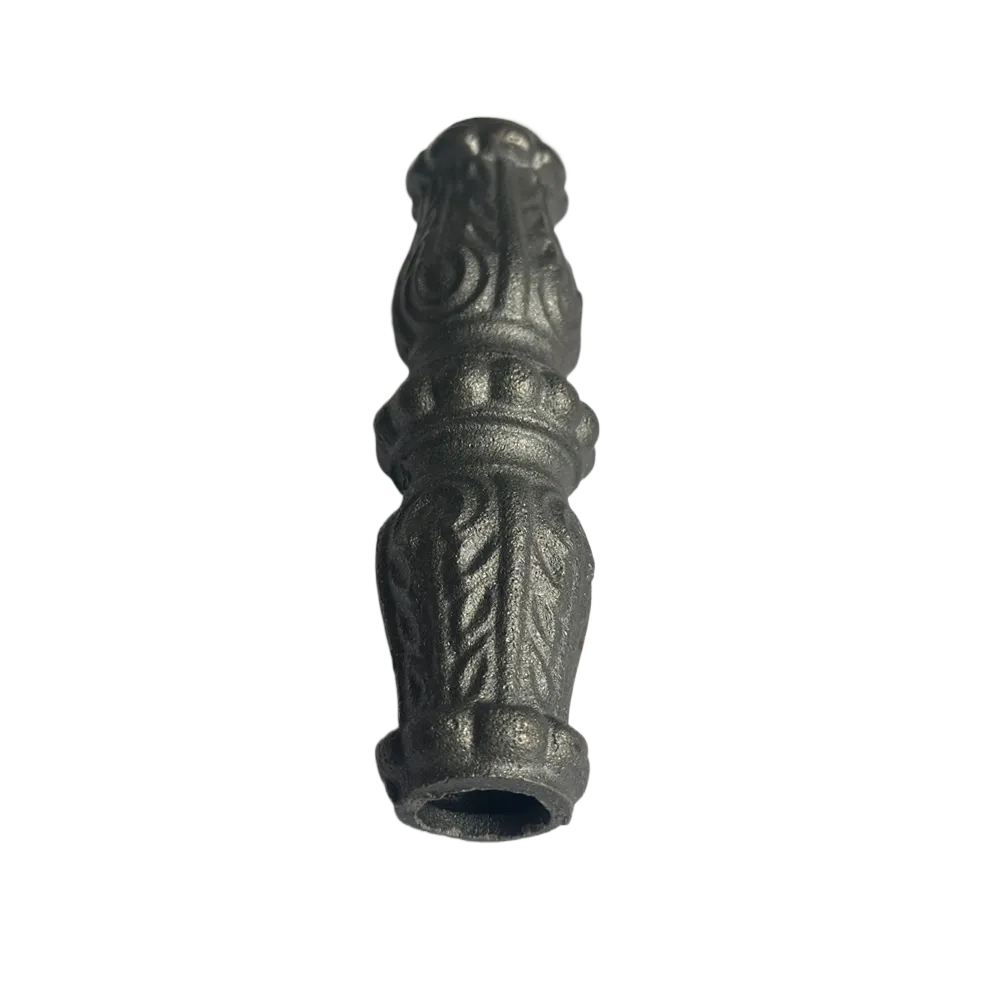
Over the years, the welding industry has consistently sought materials that provide strength, flexibility, and durability. Metal leaves provide these attributes, making them an invaluable asset in the arsenal of any professional welder. Composed of ultra-thin sheets of metal, these leaves are specifically designed to facilitate a seamless welding process, enhancing both the quality and efficiency of the work.
One of the standout features of metal leaves is their ability to reduce contamination during the welding process. The thinness of the leaves acts as a protective barrier, preventing foreign particles from entering the weld. This is particularly beneficial in industries where precision and cleanliness are paramount, such as aerospace and medical device manufacturing.
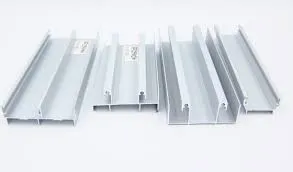
From an expert’s perspective, understanding the various types of metal leaves available on the market is essential. Metal leaves can be made from a variety of materials, including aluminum, copper, and stainless steel. Each type has its own set of characteristics and applications. For instance, aluminum leaves are lightweight and resistant to corrosion, making them suitable for automotive and structural applications. Copper leaves, on the other hand, are excellent conductors of heat and electricity, thus ideal for electrical welding projects.
The implementation of metal leaves in welding processes not only improves the structural integrity of the joints but also enhances the aesthetic appeal of the final product. Given their thinness and flexibility, metal leaves can be used in intricate designs where precise control over the welding process is required. This makes them a preferred choice for projects requiring detailed metal art or custom fabrication.
metal leaves for welding
From a professional standpoint, integrating metal leaves into welding workflows improves process efficiency. They allow for a smoother weld bead and reduce the incidence of defects such as porosity and cracking. This results in a stronger, more reliable weld, which is crucial for applications where safety and longevity are of high importance.
Trust in the use of metal leaves stems from their proven track record in various demanding environments. Professionals and experts across multiple industries vouch for their efficacy. Moreover, manufacturers of these metal leaves are continually innovating, developing specialized coatings and treatments that further enhance their performance. This commitment to quality and innovation reinforces the trust in metal leaves as a superior product in the welding industry.
It is imperative, however, for welders to receive proper training in the application of metal leaves, as their effective use requires a detailed understanding of both material properties and welding techniques. This will ensure that the benefits of these advanced materials are fully realized, leading to enhanced project outcomes.
In summary, metal leaves for welding represent a perfect confluence of strength, precision, and reliability. They are an indispensable tool for anyone in the welding industry looking to achieve superior results. Their unique properties not only address common welding challenges but also push the boundaries of what is possible in metal fabrication. For welders and industries alike, embracing the use of metal leaves can lead to greater success and innovation in welding practices.