The pantograph is an essential component in many industrial and transportation applications, serving as a connection point between power sources and moving machinery.
Understanding the intricate details of a pantograph is crucial for ensuring efficient operation and reliability. Here, we strive to provide an insightful exploration of pantograph details, emphasizing real-world experiences, technical expertise, and trustworthiness—hallmarks of authoritative content in this domain.
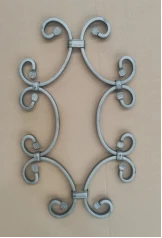
Pantographs operate primarily as current collectors, facilitating the transfer of electrical energy from overhead wires or other sources to vehicles or machinery, such as trains and trams. Their effectiveness hinges on a combination of precise engineering, material quality, and maintenance.
Materials and Engineering Precision The construction of a pantograph uses materials that can withstand environmental exposure and mechanical stress. Typically, pantographs are made from lightweight yet durable materials like carbon, copper alloys, and stainless steel, each chosen for specific conductive and wear-resistant properties. The balance in material selection is crucial; it ensures minimal friction, optimal conductivity, and increased longevity of the pantograph components.
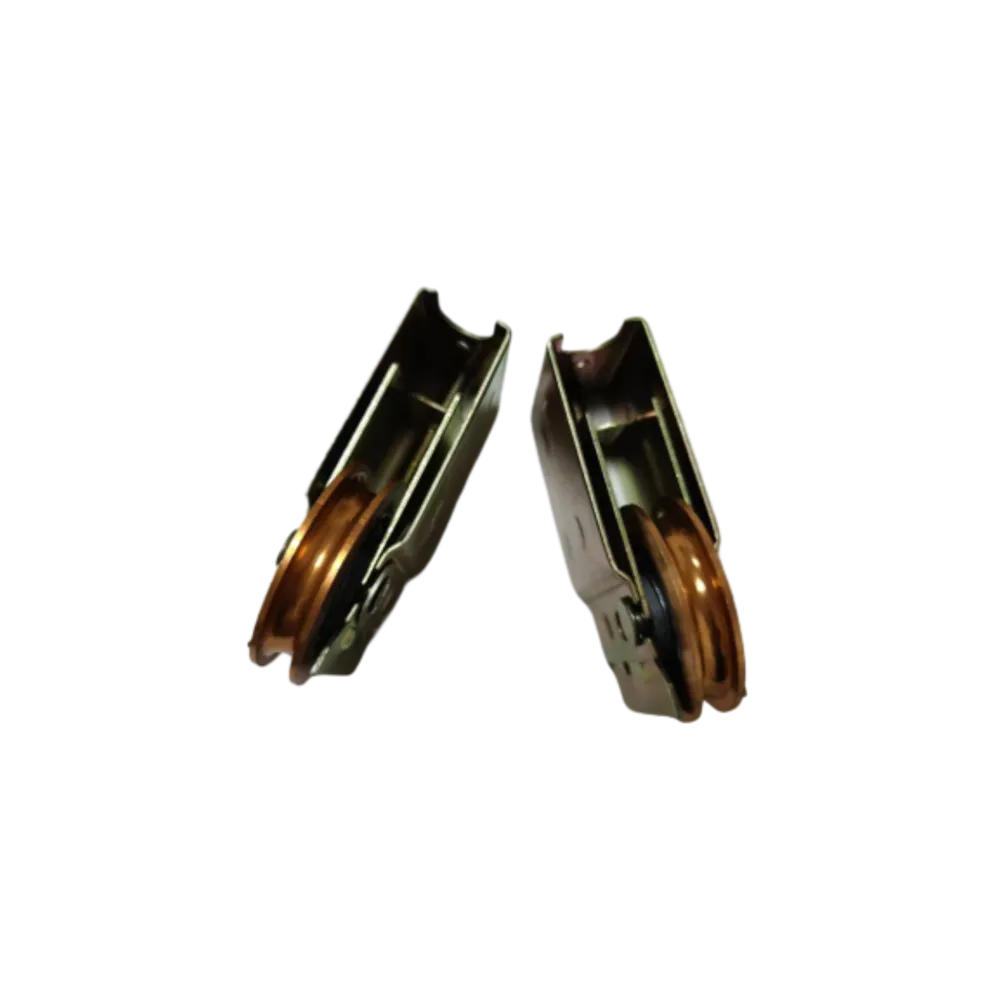
A deep understanding of the mechanical structure of pantographs is critical. Their design involves a complex architecture of arms, springs, and joints that provide the necessary upward force to maintain consistent contact with the power supply. The geometry must allow flexibility and strength, accommodating the dynamic movements of vehicles while ensuring stability.
Real-world Application and Experience Operators in the rail and transit sectors often observe that the efficiency of a pantograph is largely dependent on how well it's integrated with the vehicle's overall electrical system. Many experienced engineers emphasize the importance of calibration and alignment, noting that even minor deviations can lead to wear, sparking, and intermittent contact that may disrupt power flow. Such insights guide the regular inspection and adjustment protocols vital for optimal pantograph performance.
Pantograph data pantograph details
Moreover, environments with extreme weather conditions provide additional challenges. For instance, in regions with heavy snowfall or intense heat, pantograph designs may incorporate specific adaptations or protective measures. Experiences from various climatic regions underline the necessity for tailored solutions that take into account local operational conditions.
Professional Expertise and Innovation Continuous research and technological advancements have driven improvements in pantograph designs. Innovations often focus on enhancing durability and performance efficiency. One notable development is the adoption of smart technologies equipped with sensors and monitoring systems that provide real-time data on wear patterns, contact quality, and operational anomalies. This proactive approach allows maintenance teams to anticipate issues, scheduling timely interventions that minimize downtime and extend service life.
Furthermore, the collaboration between manufacturers, engineers, and operators has fostered a deeper understanding of the nuanced demands imposed on pantographs. Expert consensus agrees that investing in high-quality, precisely-engineered pantograph systems can significantly reduce operational costs and enhance safety.
Trustworthiness and Maintenance Strategies The reliability of a pantograph system is underpinned by regular maintenance and quality assurance protocols. Trusted manufacturers provide comprehensive manuals and support services, ensuring that operators are equipped with the necessary knowledge and tools to maintain these systems effectively. Real-world maintenance strategies often include periodic inspections, cleaning of contact surfaces to prevent debris accumulation, and the replacement of parts based on wear indicators rather than fixed schedules.
In conclusion, understanding the intricate details of pantographs involves an appreciation of material science, engineering design, environmental considerations, and the practical experiences of those who work with them daily. By integrating expert knowledge with ongoing innovations and robust maintenance practices, pantograph systems continue to evolve, providing reliable service in various industrial applications. This synthesis of expertise and experience not only underscores the importance of pantographs but also enhances their role as a critical interface between energy sources and modern mobility solutions.