Mastering the Art of Welding Hinges Techniques and Tips for Optimal Performance
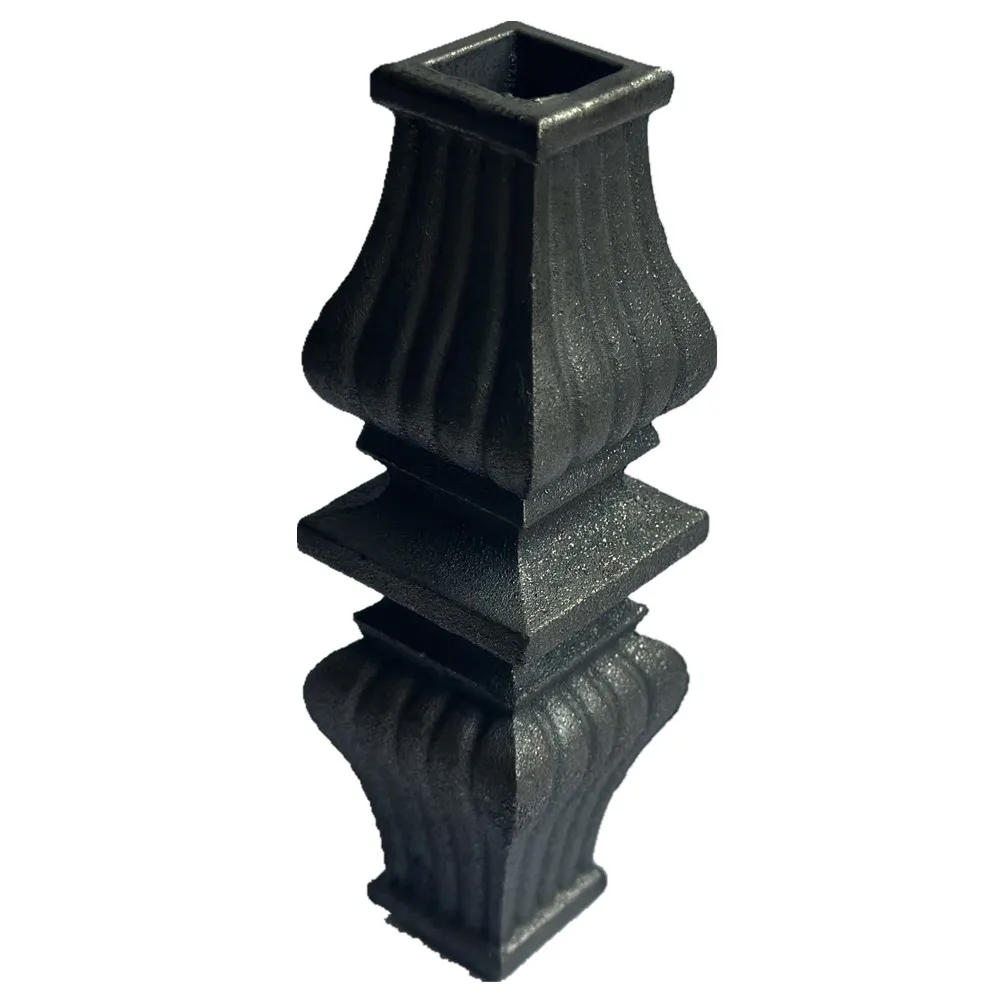
Welding hinges is an intricate craft that combines precision engineering with hands-on skill, demanding attention to detail and in-depth knowledge of materials and techniques. A hinge, seemingly a simple mechanism, plays a pivotal role in the functionality and longevity of doors, gates, cabinets, and even complex machinery. For individuals seeking to excel in this craft, understanding the nuances of welding hinges is critical to delivering results that are not only functional but also exhibit superior craftsmanship.
The allure of welding hinges lies in its fusion of technical proficiency and artistry. At the heart of this craft is the challenge of ensuring strength, durability, and seamless movement without compromising on aesthetic appeal. Whether you are a novice, an experienced metalworker, or a professional seeking to refine your skills, this guide provides insights rooted in decades of experience within the welding industry.
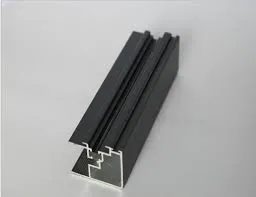
Understanding Materials The Foundation of Quality Welding
Critical to the process of welding hinges is the material selection. Different applications necessitate specific materials, each with distinct properties. Common materials include stainless steel, brass, aluminum, and mild steel. Stainless steel is favored for its corrosion resistance and strength, making it ideal for outdoor and heavy-duty applications. Brass, on the other hand, offers an elegant finish, perfect for high-end cabinetry or decorative applications. In contrast, mild steel combines affordability with strength, suitable for most general purposes.
Selecting the right material is a balance of functionality, aesthetics, and cost. Industry professionals emphasize the significance of understanding the material’s properties, as it directly impacts the welding method and operational longevity of the hinge.
Mastering Welding Techniques for Flawless Hinges
Superior hinges emerge from exemplary welding techniques. Professionals recommend arc welding, especially MIG (Metal Inert Gas) and TIG (Tungsten Inert Gas) welding, for their precision and controlled application. MIG welding stands out for its speed and ease of use, suitable for thicker materials, while TIG welding offers unmatched precision for intricate and delicate welds essential in hinge fabrication.
Each technique requires a thorough understanding of metal behavior under heat, the right choice of electrode material or filler rod, as well as the correct settings of the welding machine. Seasoned welders highlight the importance of mastering the techniques through practice and patience, reinforcing the craftsmanship required to produce faultless welds that form the backbone of durable hinges.
welding hings
Innovation in Hinge Design and Application
The evolution of hinge designs and applications demands innovation and adaptability from welders. Recent trends show a growing demand for custom-designed hinges tailored to unique architectural elements or mechanical functions. This trend emphasizes not only structural integrity but also aesthetic considerations, pushing welders to explore creative solutions and advanced technology, including 3D modeling and simulation to visualize and perfect hinge designs before actual welding.
Leveraging technology allows for experimentation in hinge design, ensuring that the final product complements both the form and function of the structure it supports. Professionals stress the importance of staying abreast with technological advancements to offer clients cutting-edge solutions.
Ensuring Quality and Durability A Commitment to Excellence
Expert welders understand that quality assurance is paramount. This begins with meticulous preparation—cleaning materials to remove impurities, ensuring precise alignment of components, and selecting the correct welding parameters. Post-welding, rigorous testing, and inspection are crucial, from stress testing for load-bearing capacity to corrosion resistance checks, guaranteeing the hinges withstand environmental challenges over time.
The commitment to quality manifests in attention to detail, adherence to industry standards, and continuous improvement. Sharing knowledge and experiences with peers, attending workshops, and obtaining certifications contribute significantly to maintaining high standards of craftsmanship and staying competitive in the field.
Conclusion Building Trust Through Proven Expertise
In the art of welding hinges, expertise and trustworthiness underscore a professional's reputation. Delivering exceptional quality hinges signifies a deep understanding of materials, adeptness in welding techniques, and a forward-looking approach to design and innovation. Clients entrust professionals who demonstrate reliability, adaptability, and a commitment to exceeding expectations. Through continuous learning and application of cutting-edge techniques, welders can cement their status as authoritative and trusted experts in the industry, ensuring their work stands the test of time both in functionality and as an exemplar of craft excellence.